Blog - January 2011
Day 7: Manufacturing Progress, No Build Meeting
Today, the FRC Build group did not meet at the lab. However, progress was still made in the manufacturing and materials procurements area. We were able to pick up the raw aluminum from Coast Aluminum in Hayward so that wheel construction can begin soon. Furthermore, Cory started setting up the CNC Mill at the lab so that we can start milling wheels soon.
Tomorrow is the VEX Tournament and the team will be meeting tomorrow night after the tournament at the lab to continue with the robot design.
Day 6: Prototyping, Programming, Design & Manufacturing Progress
Prototyping
Today, we had a large group of students working to prototype mechanisms for subsystem 2 (tube grabber. One group was working to construct a jig for testing roller prototypes. The other group worked to think up alternate solutions for tube grabbing.
Programming
The programming team met today to refine the control of the robot during teleoperated mode. Progress is being made.
Design
Today, several team members were working on the CAD Design of a part for the elevator carriage. Furthermore, later in the evening, we continued working on the mounting interaction between the elevator and the drivebase.
Manufacturing
The machining of the bearing housings is finally complete. After five long days of machining, all of the parts are done with machining. After they are deburred and polished, they will be ready for anodizing.
Day 5: Design & Programming Progress
Design
At the lab today, a number of students met to work on robot design. We spent the entire day working on Subsystem 1: Arm/Elevator. We began the day by reviewing our game objectives before proceeding to create a weighted objective table.
Elevator | 1 Joint Arm | Scissor Lift | Conveyor | 2 Joint Arm | Telescoping Arm | |
Designability (x3) | 3 | 4 | 3 | 1 | 2 | 2 |
Manufacturability (x3) | 4 | 5 | 3 | 3 | 3 | 3 |
Speed (x4) | 5 | 4 | 3 | 2 | 4 | 4 |
Accuracy (x5) | 5 | 4 | 1 | 3 | 3 | 4 |
Weight (x3) | 4 | 5 | 3 | 2 | 3 | 3 |
Weighted Total | 85 | 78 | 44 | 41 | 55 | 60 |
Using the table, we were able to rate all of the different potential superstructure designs on factors such as designability, manufacturability, weight, speed and accuracy. In the end, the Elevator and 1-Jointed arm came out way above all of the other designs so we decided to focus on those two designs.
Benefits of Elevator
|
Benefits of Arm
|
While discussing some of the pros and cons of each design, we focused especially on the designability of each design. We concluded that an arm would be much easier to design. However, because our team has built elevators in the past, we are familiar with their design and will be able to modify some of our old CAD models to work in the 2011 competition. Because of this, we decided that it would be feasable to design and build an elevator and that it was the best design for our team.
After deciding on an elevator, the team moved forward with design, looking at old robots and old CAD models. After some analysis, we started to build the new elevator assemblies, using some of the concepts used on previous robots. At the end of the day, we have completed drafts of the first and second stages of the elevator; only the carriage still needs to be completed.
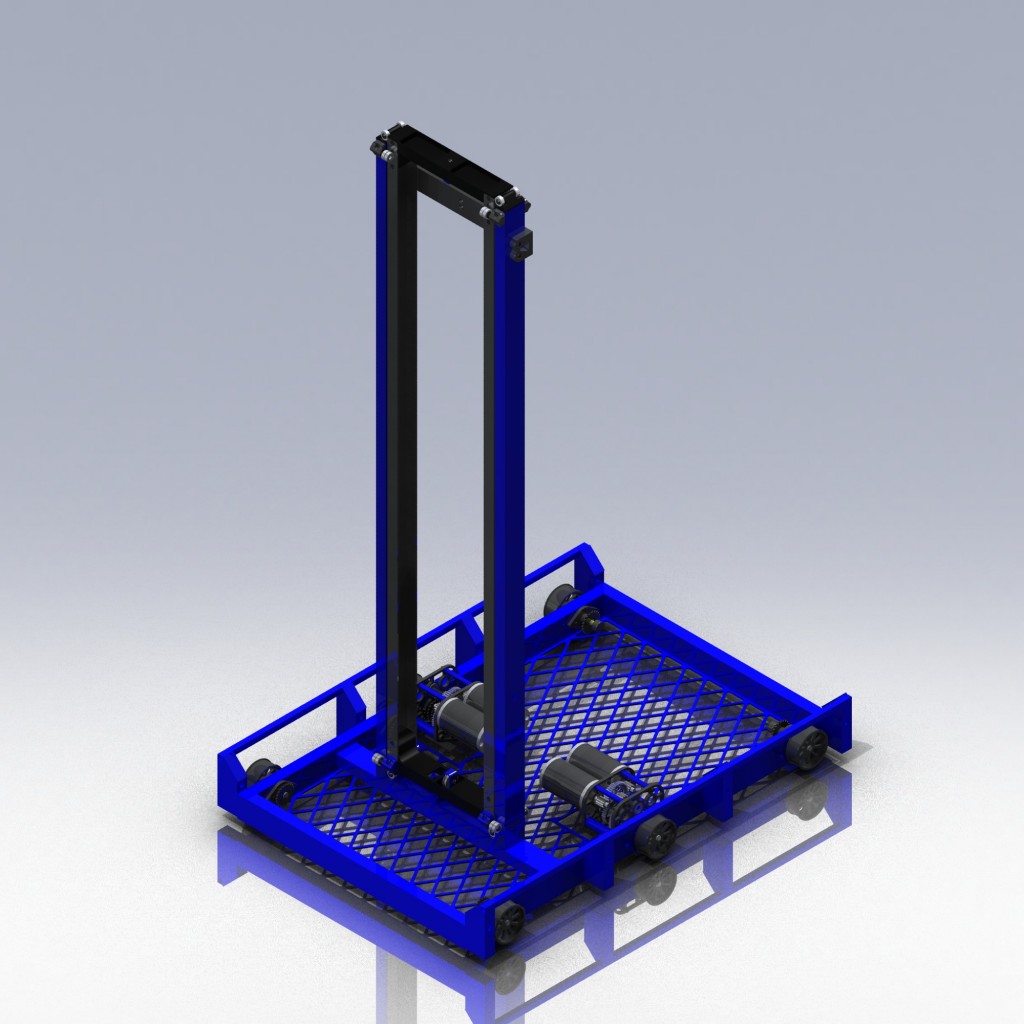
The robot design as of today. Many parts are still missing including the rear supports for the elevator.
Programming
The programming team was working hard today to perfect both the simulator and robot code.
Day 4: Field Construction, Whole Team Meeting
Field Construction
The field construction team made huge progress today. A large group of students worked hard all day to complete both the minibot pole and one grid of scoring pegs.
Whole-Team Meeting
We had a whole-team meeting at the lab today. We discussed the progress thus far in the season and decided on distinct mechanism groups that will work on prototyping and designing each mechanism. The slides are shown below.
Mechanism #0: Drivebase
Mechanism #1: Elevator/Arm to lift tubes to scoring height
Mechanism #2: Tube Grabber
Mechanism #3: Minibot
Design
The design team did not work very much today. After the whole team meeting and the field was completed, we met to discuss the benefits of elevators and arms for mechanism 1. Although no decision was made, the group seems to be leaning towards elevators for several reasons.
- We are very familiar with elevator design.
- Elevators can be extremely fast
- Precise height positioning is easier with elevators.
Here is a video of our 2007 robot and its clone, team 968, and their elevators. Although our grabbers for this year may very drastically from their grabbers, the video gives a sense for how fast these elevators can move. The elevators are able to easily move to any position in less than a second where most arms would take more time to raise a game piece.
Day 3: Field Construction, Programming, Design & Manufacturing
Field Construction
The field construction team was hard at work today working on the two elements of the game field that we are building this week. We have constructed a shopping list and hope to buy the remaining materials tomorrow.
Programming
The programming team was working hard today on teleoperated and motor control code. They have designed an interface to separated the control system (joysticks, arrow keys, etc) from the code so that the robot can be easily modified to be driven by a variety of controllers. Furthermore, they performed experiments to measure how linear the Victor Speed Controllers are in their outputs. Using MatLab, they will be able to analyze this data and derive a function to linearize the Victor outputs.
Design
The design team was hard at work today. The first order of business was the drive gearbox. After the gear ratios were finalized last night, we were able to move forward with the drive gearbox CAD which his now completed. When doing the design, we were able to develop a new way of retaining the shifter shaft between the bearings to ensure that we can shift reliably. Without motors, the wheel and bearing housing, the gearbox is less than two pounds.
In addition to working on the gearbox, a group of students worked to design and CAD the drivebase frame. After careful review of the bumper rules, we decided on a design that would support the bumpers all along the back while still being extremely lightweight. We added a heavily pocketed baseplate and put the whole thing together for a design that weighs about 30 lbs.
Manufacturing
Production continued on the first operations of the bearing housings. We hope to finish the bearing housings by Wednesday.
Lab Improvements
Today, the wired network between the lab computers was completed so that they can all share printers.
Day 2: Drivetrain Design & Manufacturing
Today, at the lab, a group of team members met to continue designing the robot drivetrain and continue manufacturing bearing blocks.
Networking & Lab Improvements
We started by networking all of the upstairs computers at the lab together. This will allow us to share printers before the computers. We were able to connect all of these using a switch generously donated by our sponsor, Vivid-Hosting. The networking will be completed tomorrow.
We also procured two power strips which were wired under the floor to provide power to two upstairs tables for laptops. Previously, the lab did not have a good place for laptops to work.
Manufacturing
Manufacturing on the bearing blocks continued today. Progress is being made and the manufacturing will continue into the next few days.
Design
Today, we discussed and decided on several key aspects of the drivetrain.
The first topic of discussion was wheel size. Several team members brought up the idea that with such a flat game field, we could potentially go to wheels even smaller than 4″. Although we quickly ruled out 3″ wheels due to lack of ground clearance (~1/4″ clearance), we were interested by the prospect of 3.5″ wheels which would lower our center of gravity slightly and could decrease drivetrain weight by more than one pound. Furthermore, because less gear reduction is needed with smaller wheels, the weight of the spinning components could be decreased by up to 20%, leading to a potential significant increase in robot acceleration. However, some team members had reservations due to the decreased ground clearance in the move from 4″ to 3.5″ wheels.
To come to a consensus, we created a weighted objective table to weight some of the pros and cons of each design. After much deliberation, the table resulted in almost a tie so we continued to discuss. In the end, it was decided that any problems caused by the decreased ground clearance (1/4″ lower) of the 3.5″ wheel system could be avoided so we decided to move forward with the lighter 3.5″ wheel design. This caused the outer bearing blocks to need edits so that they would not interfere with the newer, smaller wheels.
Benefits of 3.5″ Wheels
|
Benefits of 4″ Wheels
|
The second topic of discussion was robot speed. After yesterday’s strategy session, the whole team was in agreement that having a fast and maneuverable robot would be key to successful performance in Logomotion. After deciding on small, 3.5″ diameter wheels, we also knew that these smaller wheels would not require as large of a gear reduction as has been present in past robots.
With the ability for a smaller gear reduction, we started with our gear ratios from last year and worked with them to both speed up the robot and minimize the use of large gears to decrease robot mass and increase acceleration. In the end, we found a set of ratios that we liked that will both allow for the fastest 254 robot ever built and for smaller and lighter gears while still maintaining a slower low gear.
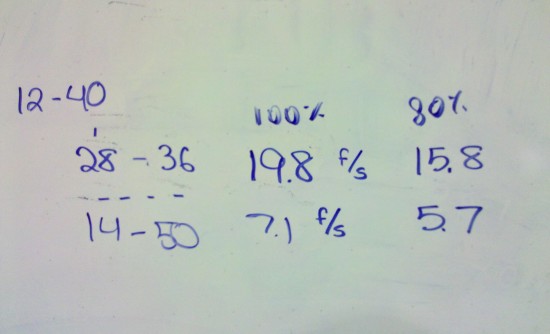
Finalized gear ratios for the 2011 robot. Robot speeds are estimated for 3.5" wheels in ft/sec at 100% and 80% efficiency. The first line represents the common reduction. The second and third lines correspond to the secondary reductions for High and Low Gear.
Finally, today was our deadline to finalize the gearbox shafts to be sent out for manufacturing by sponsor Pacific Precision. All four of the shafts were updated and finalized by a team of students. All drawings were checked by team leaders and mentors and were sent to manufacturing.
FRC Season Day #1
Today was an extremely productive day at the lab. We built a significant part of the field, tested the game elements, began design, started manufacturing and continued to work on programming.
Field Construction
As soon as we got to the lab, a large group of team members got started building a replica of the most essential field elements – a rack and a tower. We intend to build enough of a low-cost field for testing and the NASA Robotics Alliance Project will purchase a complete field for the west coast in the coming weeks. The field will stay at our lab during the build season but will travel around the state for various off-season competitions afterwards.
Game Element Testing
After we had a basic understanding of what the rack was going to look like, we moved forward with game piece testing. We experimented with how far the tubes could be thrown and discovered that a well-trained human player could likely throw tubes across the entire field.
Programming
The programming team was working hard all day. They began the day by installing the new versioins of the programming software and then spent the day getting Onslaught to drive under driver control. The simulator group was working on data logging, 3d modeling and collision detection.
Design
After dinner, a group of team members met to discuss robot design. We immediately decided on a wheeled robot and decided that at least 6 wheels would be best for maneuverability. To save weight, we all agreed that it was not practical to consider building a robot with more than 8 wheels. We also decided that we would like a two-speed drivetrain with a high gear to quickly traverse the field and a low gear to push other robots out of the way if necessary.
When looking at the game field, we were very worried by a 1/4″ tall plate under the carpet surrounding each tower. The concept of a 6 wheel drive or 8 wheel drive drivertrain with dropped center wheels relies on the fact that not all of the wheels will be on the ground at all times to improve turning. We were worried that when in proximity to the plate under the field, more wheels would be in contact with the carpet which could inhibit turning. We thought that this might be a greater issue with the six wheel drive robots than with eight wheel drive robots, but decided to test to make sure.
We put down a metal plate under carpet and tested it with both 8 wheel drive and 6 wheel drive robots. It was determined that the 8 wheel drive robots drove considerably better when in proximity with the plate when in high gear. However, in low gear, both robots had great performance as if the small bump wasn’t even there.
We took the data from our tests and moved on to discuss how important turning near the towers would be in high gear. It was determined that the only time turning near towers would be very necessary is when lining up to deploy the Minibot. We decided that this is only for about 5 seconds of the match and that there is no reason to not just use low gear during this time.
After we decided that it was not important to be able to turn in high gear near the towers, we all decided to move forward with a six-wheel drive robot. Everyone in attendance voted that the benefits of saving up to 3 pounds outweighed the drawbacks of potential limited turning in high gear when in close proximity to the towers and agreed that a six-wheel robot would be best.
The next topic that was discussed was traction. Although with ideal physics, contact area with the ground does not affect traction, it was determined through observation that due to the tread material interlocking with the carpet fibers, more contact area does indeed result in greater traction. Because of this, we discussed moving to slightly wider wheels in order to increase the contact area with the ground. We were worried that wider wheels could negatively affect turning so we decided that the robot should be designed with thin wheels (similar to what we have used before) but should be compatible with wider wheels if necessary.
Finally, we discussed speed. The consensus was that we want to be able to drive fast. However, no decision was made on exact robot gear ratios or speed. Both will be discussed and finalized tomorrow.
Manufacturing
As soon as it was finalized that we would be building a wheeled robot, manufacturing began on the bearing blocks to support the wheels. All of the stock for the bearing blocks was cut and the first operation began on the outside bearing blocks. We expect to complete the first operations on all of the bearing blocks tomorrow.
FRC Kickoff Meeting Review
The 2011 FIRST Robotics Game Has been Announced: Logomotion
Team 254 met at Bellarmine in the morning to discuss the game.
Here are the notes from the FRC Kickoff Meeting.
Robot Attributes for Successful Gameplay:
- Minibot
- Score on Top/Middle/Low Pegs
- Blocking
- Uber Rings
- Traverse Field Quickly
- Logo
- Rearrange Tubes
- Pickup from Floor
- Rings from Human Player
- Follow Lines
Obstacles to Successful Gameplay:
- Broken Partner
- Minibot Fall
- Opponents Block (Goals and Pickup Stations)
- Popped Tubes
- Wrong Logo
- Partners in Way
- Bad Visibility
Methods of Scoring and Defense:
- Minibot *
- Scoring Tubes Everywhere *
- Ubertube *
- Blocking
- Wall
- Fast/Maneuverable *
- Pick from Ground *
- Pick from Human Player
* means that the method was determined to be Essential.
The Day Before Kickoff
It’s the night before kickoff and what a productive day it’s been.
The day started out with us ordering over 250lbs of Aluminum from Coast Aluminum in Hayward. The metal will be used to construct the robots for Team 254 and Team 1868. Although we don’t yet know the game and don’t know what the robots will look at, we are predicting that they will have metal frames, so we bought the material to build frames. After it was ordered, EJ and Sunshine drove up to Hayward in a NASA truck to pick up the material.
At the lab, other team members worked to put together a final list of consumable lab supplies that NASA will purchase. Most of the items on the list were ordered today and the remainder will be ordered over the weekend.
Also at NASA, several programmers from both the simulator group and the robot group were working on various tasks in preparation for the busy robot build period.
Finally, several students worked hard to put the finishing touches on the NASA lab to prepare it for build. The couches were cleaned and brought back upstairs and the welding table was polished to remove rust. The field was vacuumed and shelves were organized.
9 Hours Till Kickoff
Go Poofs!
T-Shirts Ordered
The team T-Shirts are ordered and should be ready just in time for the Bellarmine VEX Tournament.
Cleaning up the Lab
Today at the NASA lab, several students and mentors were working together to clean up the workspace and prepare for the build season.
The computer workstations upstairs were put together after the painting. All of the wires were nicely ziptied and the process of software updates began. In the next few days, we need to update all of the computers with current versions of SolidWorks and other crucial software. Furthermore, we need to build a wired network at the lab so that we can share printers between the computers. On the white boards, vinyl stickers were cut to label each teams’ white board.
Downstairs, Devastator was prepared to be removed from the NASA lab for semi-permanent storage at Bellarmine so that it can be used for team outreach events and demonstrations. This freed up space under the south stairwell so that we were able to move the vertical bandsaw into its own cavity, improving the safety of the workspace. We also spread out the sanding and grinding area and moved a wall-mounted shop vac out of the sheet metal area into the sanding and grinding area so dust and debris can be vaccumed up.
In the sheet metal and welding corner of the lab, work continued to prepare the area. We re-arranged the extremely heavy equipment, putting the welder in a position so that its cord could reach the outlet and so that it is easily accessible. To accommodate these changes, we had to slightly adjust the positioning of the sheet metal shear and break and move the large arbor press into the machine shop.
In the general work area, we continued cleaning and organization and also began resurfacing the workbenches so that they have nice, smooth surfaces to work on.
Everything is coming along great and we are very excited for the Saturday FRC kickoff.
Floor Painting Complete
Today the mezzanine floor was completely dry which allowed the tables and chairs to be moved back upstairs. A few students were present and helped set up the computers and get things ready for the upcoming FRC build season. The office supplies and mentors cabinets were also sorted, leaving only a few tasks left to be completed tomorrow and Thursday.
254D High Hangs!
VEX Team 254D has been working hard since their last tournament to improve on their design as much as possible. After a lot of work, their robot successfully high hangs on the ladder for a whopping 20 points!
All of the Team 254 VEX Teams are busy pulling together their robots before their Thursday deadline.
Lab Floor Painting & Cleaning
Today, more team members met at the NASA lab to apply a second coat of paint to the floor on the upstairs mezzanine. The newly painted surface looks great and we will move the furniture upstairs tomorrow once the paint dries. Furthermore, we mopped and vacuumed the floor downstairs and organized the tool chest, the white shelves and the cabinet in the machine shop.
Lab Floor Painting
Today, several team members met at the NASA lab to paint the floor of the upstairs mezzanine. Two weeks ago, we sanded the floor to remove the chipping paint and last week new paint was able to be purchased. To prevent chipping, we are using a urethane-based industrial paint. Tomorrow, we will meet again to apply a second coat of paint.